PROJECTS
1. Agri-Bot

-
Agri-bot is a di-wheel machine used for decreasing farmers' efforts in plowing, watering, etc. This di-wheel is controlled by an RF( radio frequency) controller. Agri-bot comprises an actuator, Arduino UNO, micro-controller, stepper motor, and lead-acid battery as well.

-
Testing of the actuator with different RPM values to check the functionality of the actuator.

2. Design and Analysis of Lengthwise Gradient Honeycomb Core for obtaining graded beam properties

-
Honeycomb structures are natural or artificial structures that offer more strength and are low weight structures relatively. In this study, different types (different cell orientations) of hexagonal honeycomb structures are designed, and geometrical dependent properties are derived to analyze the trend when dimensions of cells in honeycomb structures are increased gradually. The diagonal length of cells in honeycomb was varied from 12 mm to 21 mm and mechanical properties like total deformation were evaluated when the honeycomb structure was made to act like a cantilever beam with a point load at its free end. Similarly, a gradient honeycomb structure was designed and mechanical properties like total deformation were evaluated when subjected to point load at its free end by fixing one the other end of the structure(cantilever). On average, gradient honeycomb structure deforms 15.43% less than the regular honeycomb structure. Drop-over impact tests were simulated in the Ansys workbench by dropping a stainless steel sphere onto an aluminum gradient honeycomb structure to evaluate energy absorbed at different times during the impact. The analysis of simulated results confirms that lengthwise gradient (variation of cell size along the length) honeycomb structures (both vertical and horizontal oriented) possess both bending resistance and good energy absorption abilities.

-
The above video is a simulated video to test impact loading on Honeycomb structure with cell variation along the core length. The above picture is energy probe analysis performed in Ansys (Explicit Dynamics). The green line and pink lines are kinetic energy and internal energy, respectively generated with the sphere's impact (Structural steel) on Honeycomb Structure (Aluminium). The maximum values of internal and kinetic energy are 11.242 Joules and 13.718 Joules, respectively. The minimum value of internal and kinetic energy is 0 joules and 2.836 Joules, respectively.
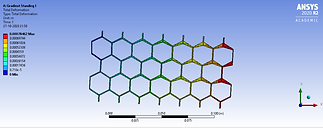.png)

-
The above two images are simulation screenshots of the total deformation of the Honeycomb structure when one end of it is fixed. A point load of 100N is applied to another end of the Honeycomb Structure. The first picture is the Gradient Honeycomb structure, which offers more bending resistance than the regular honeycomb structure, the picture on the bottom right.
3. DESIGN AND SIMULATION OF CONVERGENT LPG BURNER CONTAINING DIFFUSER
-
Many LPG burners have been existing in the market and coming up with new designs and different efficiencies. But this is a new mode of design where only holes are made convergent and fuel is supplied at the same flow rate and volume. So, this new design is made in SOLIDWORKS and simulated in ANSYS. Many papers are taken as a reference and hence simulated with proper conditions which are similar to the surrounding media in a kitchen. A series of simulations was performed and found that many different values were obtained at different angles. A diffuser, which can create a swirling effect to the burner and create the combustion more effectively, is also implemented. To know where the highest efficiency can be achieved, a water boiling test has to be performed to fabricate this prototype with brass metal.

-
Design and simulation details cannot be shared as a patent has been filed with the design. (Yet to be granted)